In 2015 alone, businesses lost $1.1 trillion due to poor inventory management. Thatโs the size of nearly the entire Australiaโs GDP that year!
With the rise of online shopping, we can expect losses to go up further over the coming years.
Now that might not be a worrisome amount for big corporations, but for small and medium-sized businesses that amount might be the difference between success and failures.
If you are running an eCommerce store, you might just be on the right page.
If you own a business, a solid inventory management system should be your top priority. Otherwise, you will find yourself in a shortage of products at the time of an important sale!
Trust us, we have seen many cases where an eCommerce store has a hit product, but because of the lack of inventory management is struggling to fulfill orders.
Ultimately, it hampers the brand image and you lose out on potential sales.
Take a tour with us to see how an inventory management system can lead to improved accuracy, streamlined order management, prevention of stockouts, enhanced customer service, and increased sales.
- Tips to improve WooCommerce inventory management
- 1. Create a detailed inventory policy
- 2. Track inventory movements
- 3. Set up reorder points
- 4. Implement a just-in-time inventory system
- 5. Use a warehouse management system
- 6. Conduct regular inventory audits
- 7. Use a reporting tool
- 8. Be proactive: Take action before problems occur
- 9. Don't forget about customer service
- 10. Use technology to your advantage
- Top inventory management plugins for WooCommerce
- Final words
- WooCommerce Inventory Management – FAQs
What is WooCommerce inventory management?
WooCommerce inventory management refers to the process of overseeing and controlling the inventory of products within a WooCommerce-based online store.
It involves efficiently tracking stock levels, managing product variations, handling incoming and outgoing inventory, and ensuring accurate inventory data across different channels.
That means it is the number of products you have in stock.
Why do you need a WooCommerce inventory management system?
Here are some key reasons why you need a robust inventory management system for your WooCommerce store:
Improved inventory accuracy
By implementing a reliable inventory management system, you can easily maintain accurate stock levels. You will get updates in real-time into your inventory that will help you prevent overselling or underselling.
It will also minimize the risk of stock discrepancies and associated customer dissatisfaction.
Improved order management
Efficient inventory management enables you to streamline order fulfillment processes. With accurate information, you can promptly process orders, avoid backorders, and improve overall customer satisfaction.
Prevention of stockouts
Inventory management will help you to set up reorder points and automated alerts when stock levels reach a certain threshold.
This proactive approach helps prevent stockouts, ensuring that popular products remain available for customers.
Improved customer service
Accurate inventory management leads to better customer service. By having real-time stock information, you can provide accurate product availability, and estimated delivery dates, and prevent delays or cancellations.
Increased sales
Optimized inventory management can positively impact your sales. By avoiding stockouts and effectively managing product variations, you can meet customer demand, drive repeat purchases, and enhance customer loyalty.
In fact, when comparing customer loyalty vs customer retention, efficient inventory practices support both by ensuring consistent product availability and a reliable shopping experience.
Unlock the Ultimate WooCommerce Store Guide!
Want to build a successful WooCommerce store in 2025? Get our FREE, exclusive step-by-step video course created by the CartFlows team.
Ultimate WooCommerce Store Guide!
Want to build a successful WooCommerce store in 2025? Get our exclusive, step-by-step video course.
Tips to improve WooCommerce inventory management
Now that we understand the importance of efficient inventory management in WooCommerce, let’s explore some practical tips to enhance it:
1. Create a detailed inventory policy
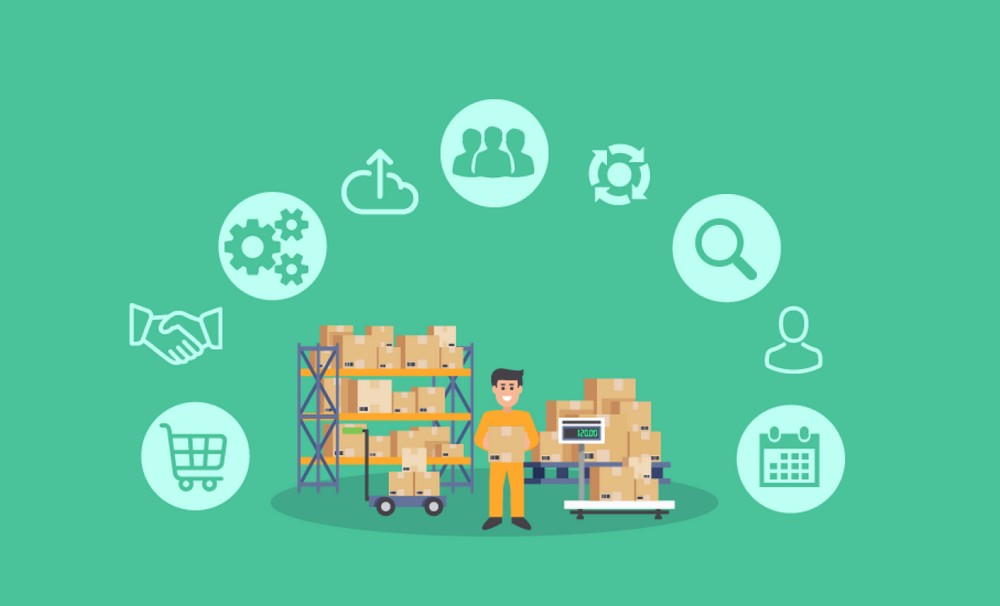
You ideally need a detailed inventory policy that outlines the procedures for managing inventory within an organization.
It should include the factors such as inventory levels, replenishment methods, order quantities, lead times, and safety stock requirements.
The policy should also align with the company’s overall business objectives and factors like demand forecasting, sales patterns, and production capabilities.
Develop an inventory policy that outlines your inventory strategies, stock thresholds, and order processing timelines.
2. Track inventory movements
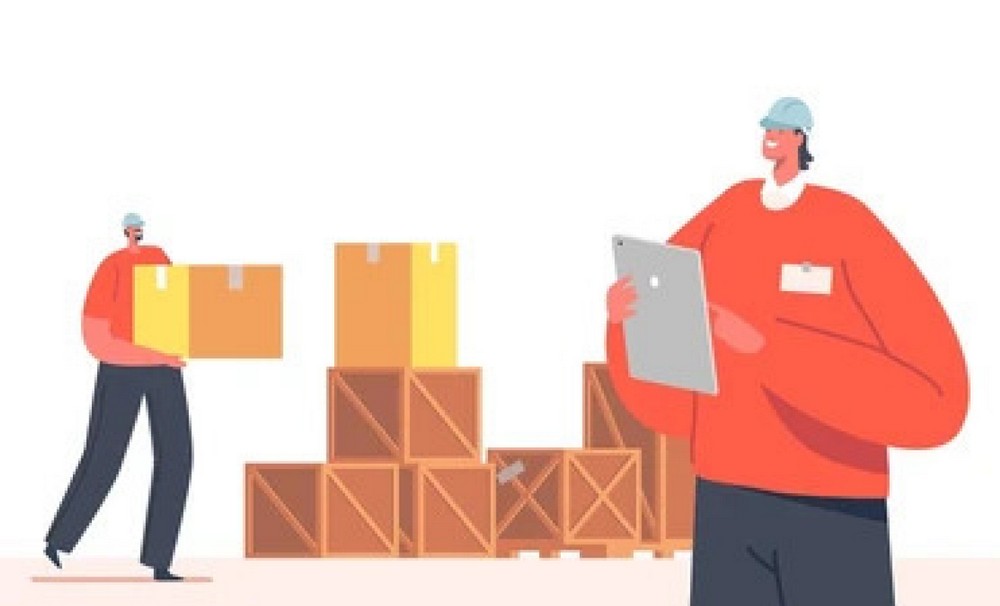
Implement inventory tracking mechanisms to monitor incoming and outgoing stock accurately.
Utilize barcodes, scanners, or inventory management software to streamline the tracking process and minimize errors.
Here is a list of the business benefits of tracking inventory:
- Improved inventory accuracy
- Efficient replenishment
- Cost reduction
- Improved customer service
- Demand forecasting and planning
- Fraud and theft prevention
- Streamlined operations
- Data-driven decision making
- Regulatory compliance
3. Set up reorder points
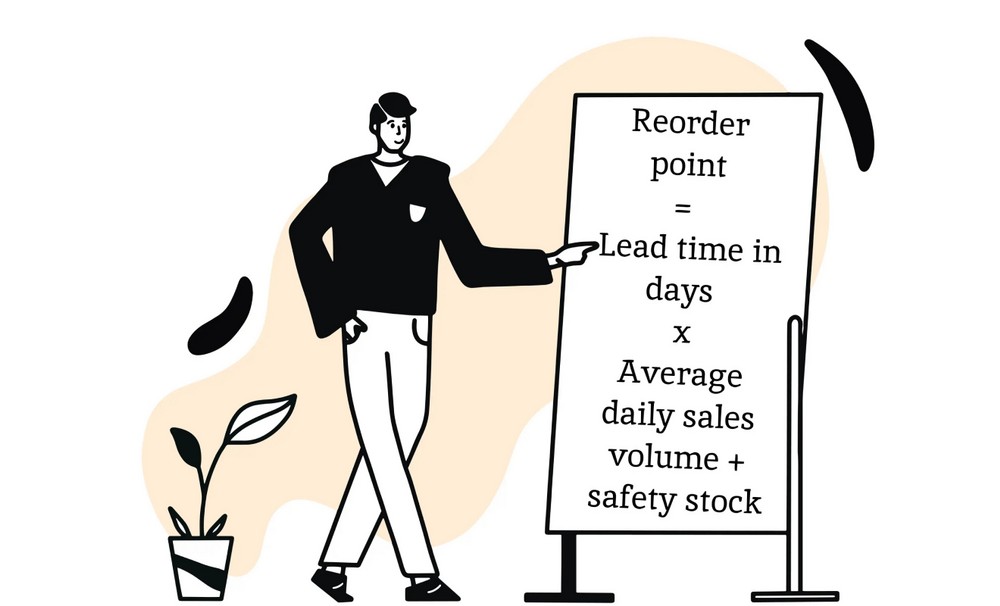
Reorder points are predetermined inventory levels that trigger the need to reorder products.
They are typically set based on factors such as lead time, demand variability, and desired service levels. When inventory levels reach the reorder point, it signals the need to initiate the replenishment process to avoid stockouts.
Determine optimal reorder points for your products based on historical sales data, lead times, and customer demand.
This ensures that you replenish inventory at the right time, avoiding stockouts or excess inventory.
4. Implement a just-in-time inventory system
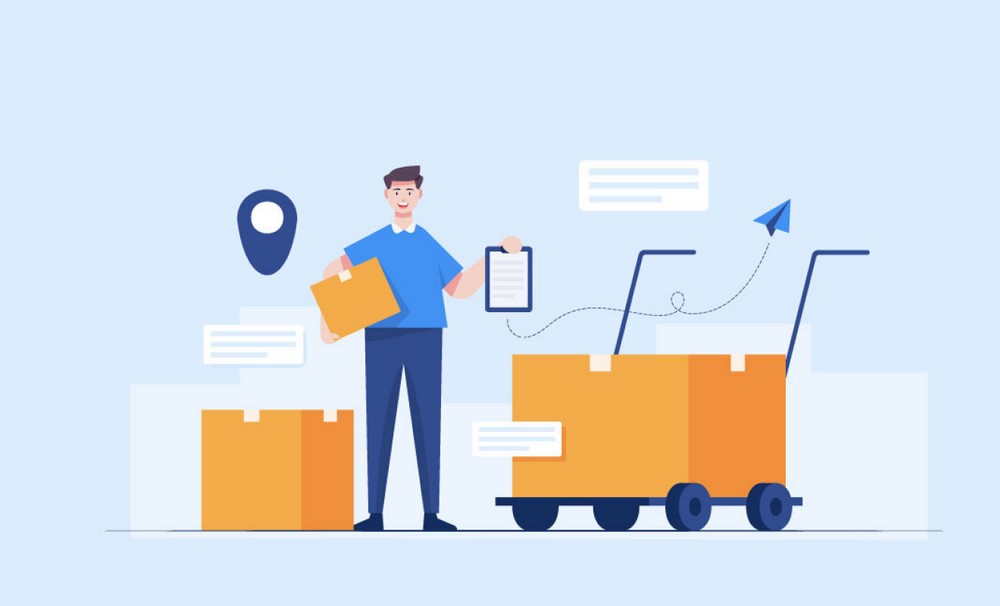
A just-in-time (JIT) inventory system aims to minimize inventory holding costs by synchronizing the delivery of raw materials or finished goods with production or customer demand.
Under JIT, inventory is replenished only when it is needed, reducing excess stock and associated costs.
This system requires accurate demand forecasting, strong supplier relationships, and efficient logistics management. In fact, many businesses are now using AI consulting for logistics to improve demand forecasting accuracy, optimize supply chain coordination, and ensure smoother just-in-time operations.
Consider adopting a just-in-time inventory approach where inventory is ordered and received shortly before it is needed for fulfillment.
This method minimizes holding costs and reduces the risk of obsolete inventory.
5. Use a warehouse management system
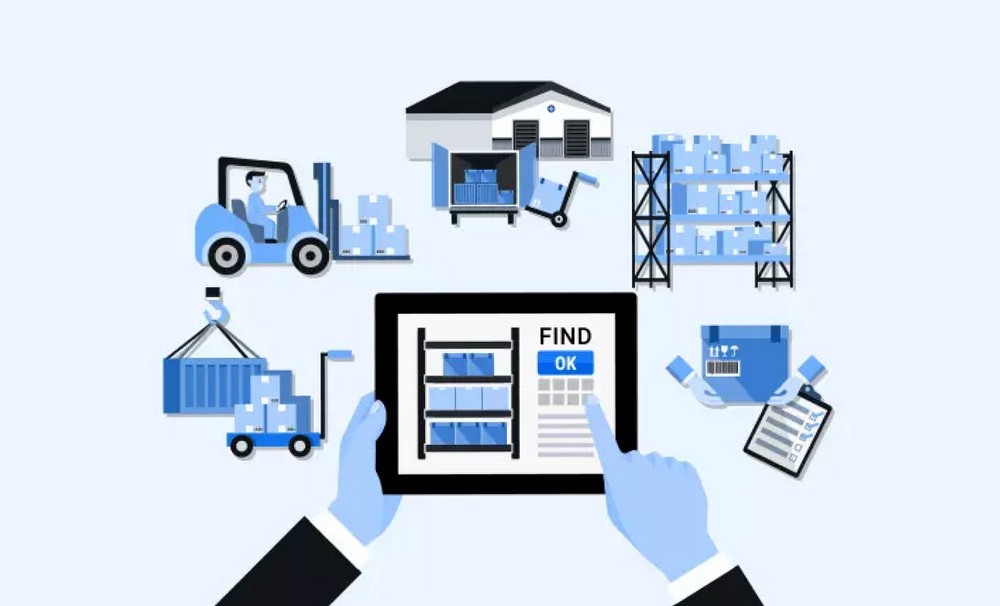
A warehouse management system (WMS) is a software application that helps manage and control warehouse operations. It provides real-time visibility into inventory levels, facilitates order processing, optimizes storage space, and streamlines workflows. These capabilities are essential components of effective project management in logistics, 3pl costs, and supply chain operations.
A WMS can automate tasks such as receiving, picking, packing, and shipping, improving efficiency and accuracy.
It may be worth investing in a warehouse management system to efficiently manage your inventory. When it comes to maintaining optimal stock levels and efficient fulfillment processes, exploring third-party logistics solutions can be invaluable. They provide a strategic approach to storage, inventory management, and shipping as a cohesive unit. It can help optimize storage space, streamline picking and packing processes, and provide real-time inventory visibility.
6. Conduct regular inventory audits
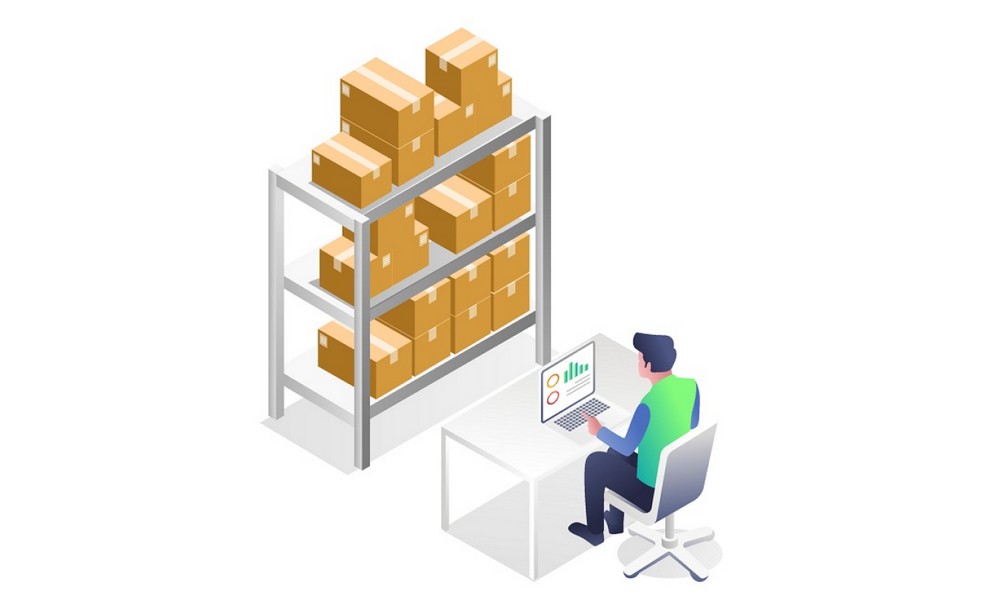
Regular inventory audits involve physically counting and reconciling the actual inventory with the recorded quantities in the system.
Audits help identify discrepancies, such as stockouts, overstocking, or inventory shrinkage due to theft or damage. By conducting audits at regular intervals, organizations can maintain inventory accuracy and ensure reliable data for decision-making.
Regular inventory audits can identify and rectify any discrepancies between physical and recorded stock levels. This process helps maintain accuracy and reduces the chances of stock-related issues.
7. Use a reporting tool
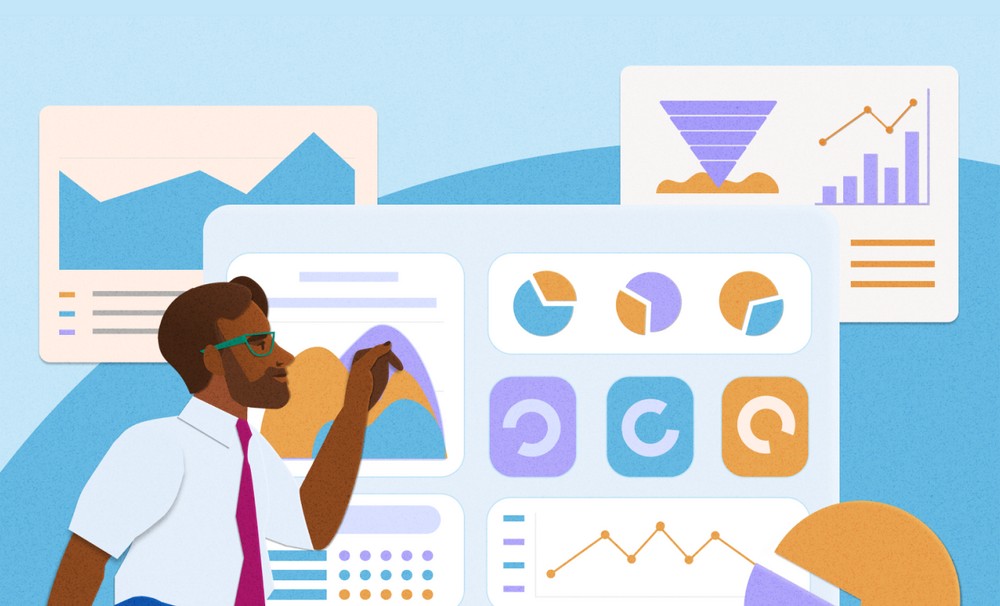
A reporting tool allows organizations to generate comprehensive reports and analyze inventory data. It provides insights into inventory levels, turnover rates, stockouts, lead times, and other key performance indicators (KPIs).
Reports help identify trends, forecast demand, optimize inventory levels and make informed business decisions.
Leverage reporting tools or inventory management software to generate insightful reports on sales, stock levels, and product performance. These reports can assist in making data-driven decisions and forecasting future inventory needs.
8. Be proactive: Take action before problems occur
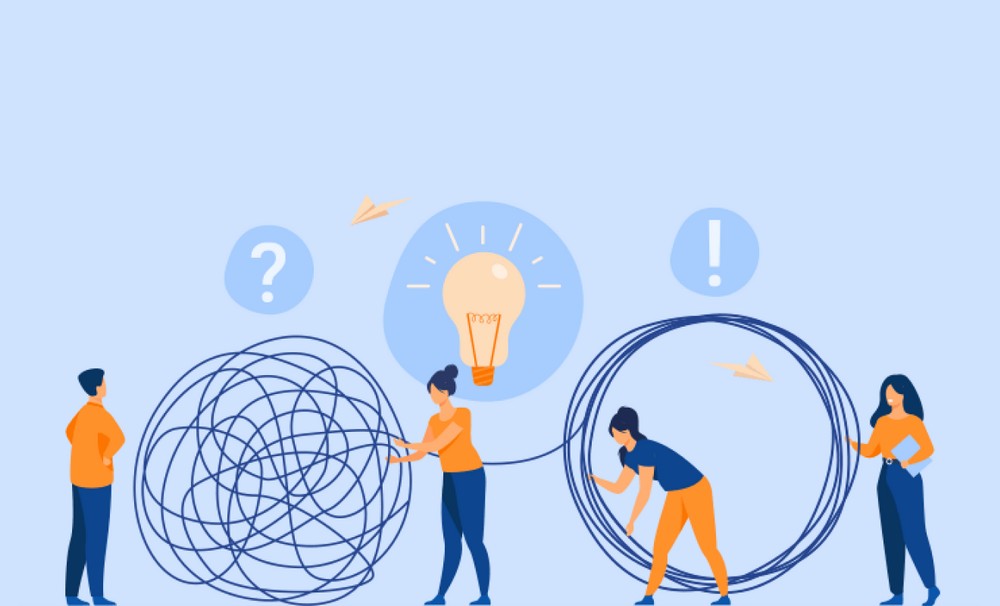
Being proactive involves taking preventive measures to address potential inventory-related issues before they occur.
This can include proactive demand forecasting, identifying bottlenecks in the supply chain, maintaining buffer stock for unexpected spikes in demand, and implementing contingency plans to mitigate risks.
Monitor your inventory regularly and proactively address issues such as slow-moving or obsolete stock, stock discrepancies, or supplier delays.
Swift action can prevent potential disruptions and minimize customer dissatisfaction.
Itโs easier to do this if you have a plan in place to guide your choices when the time to act arrives. You can do this by taking the best action plan template for your needs, and adapting it to cover the specific scenarios you expect to encounter in an inventory management context. Having a framework to follow avoids missteps.
9. Don’t forget about customer service
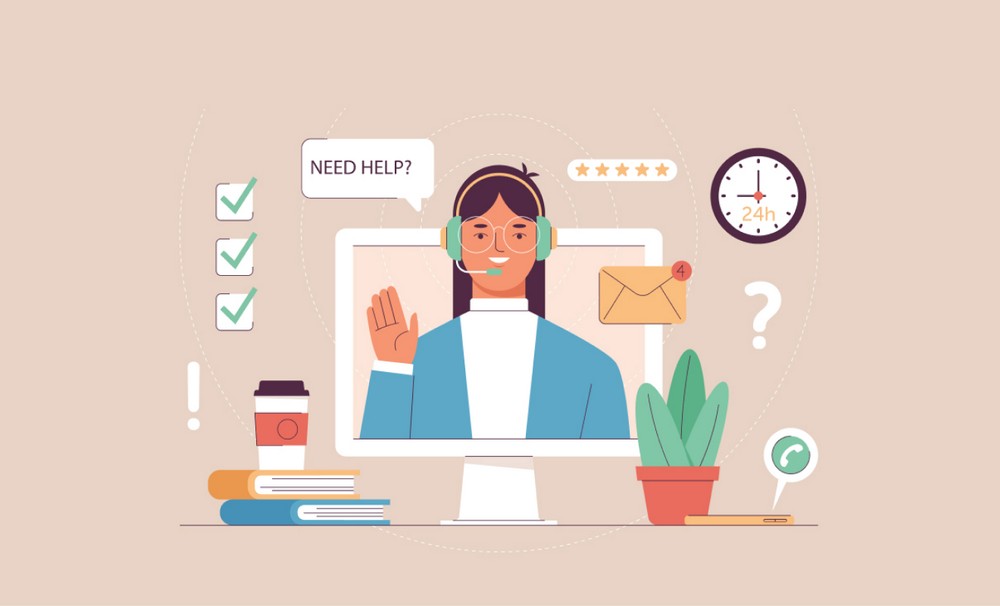
An effective inventory management system considers customer service a priority. It ensures product availability, timely order fulfillment, and accurate delivery.
By optimizing inventory levels, organizations can meet customer demands promptly, reduce lead times, and improve overall customer satisfaction.
Inventory management processes can be aligned with your customer service goals. It can help update product availability on your website, provide accurate shipping estimates, and proactively communicate with customers regarding any inventory-related issues.
10. Use technology to your advantage
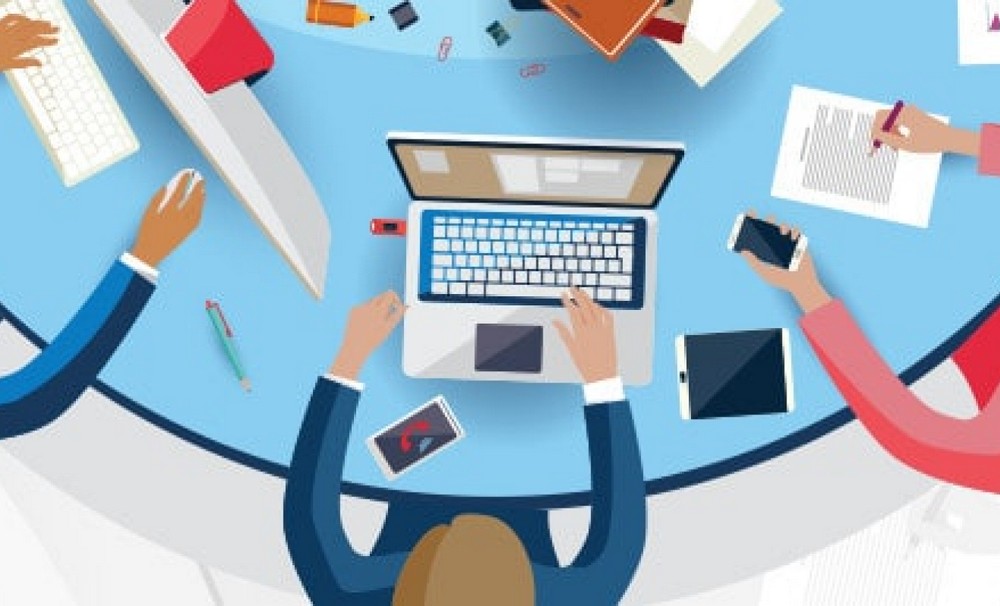
Leveraging technology can significantly enhance inventory management. This includes utilizing inventory management software, barcode scanning, RFID systems, automated data capture, and integration with other business systems like enterprise resource planning (ERP).
Technology streamlines processes, reduces errors, improves data accuracy, and enables real-time visibility into inventory movements.
Leverage technology solutions such as WooCommerce inventory management plugins, integrations with third-party systems, and automation tools. If you’re looking for social media automation using WooCommerce, you can refer to this awesome guide from Nuelink!
These can simplify your inventory management tasks and provide real-time insights for effective decision-making.
We have also got a bonus part where you can find the best inventory management plugins.
Top inventory management plugins for WooCommerce
So you now know why inventory management plugins are necessary for your WooCommerce store.
We are now going to list the top inventory management plugins so that you can easily manage your inventory.
They include:
- Stock Sync with Google Sheets for WooCommerce
- ATUM WooCommerce Inventory Management
- Smart manager for WooCommerce
- WP Inventory Manager
- WooCommerce out of stock manager
Stock Sync with Google Sheets for WooCommerce
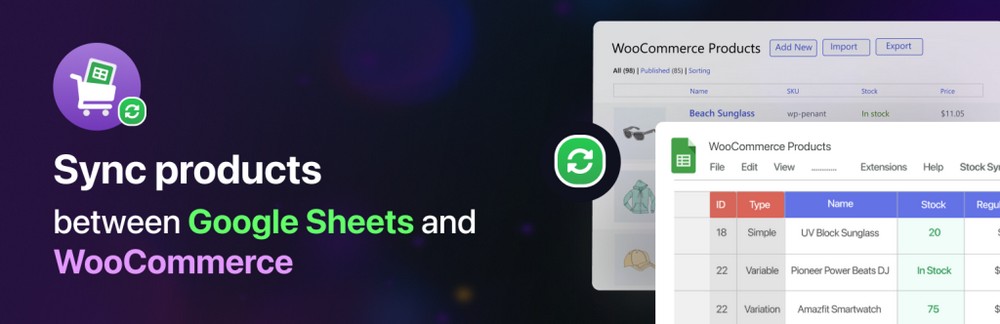
Stock Sync for WooCommerce with Google Sheet is a popular inventory management plugin for WooCommerce. It stands out as one of the most advanced systems available, offering seamless two-directional sync with Google Sheets.
This powerful stock manager plugin allows you to make edits to various aspects of your store directly from your linked spreadsheet, ensuring automatic updates on your main eCommerce site.
The plugin not only streamlines inventory management but also keeps your customers engaged by providing real-time inventory updates on your website.
Features:
- Easily export products to Google Sheet
- Support for variable products
- Update almost everything
- Auto-sync with a two-directional path
- Manually edit or remove products from the sheet
- One-click manual sync button
ATUM WooCommerce Inventory Management
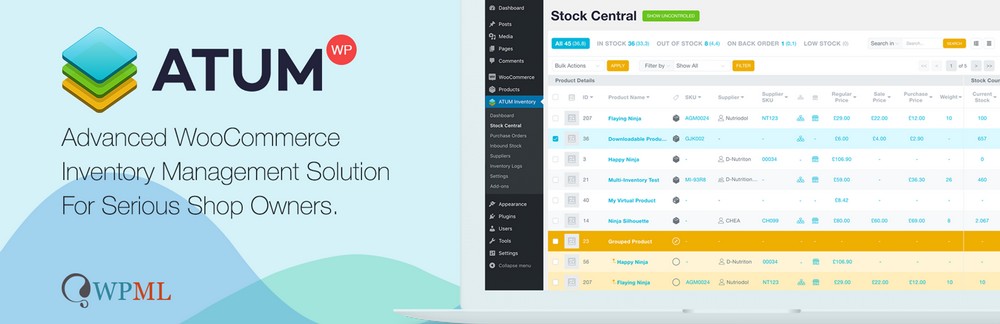
ATUM is a feature-rich inventory management plugin designed specifically for WooCommerce. It offers a comprehensive set of tools to effectively manage and control your inventory.
Seven key features of ATUM:
- Stock central
- Inventory control
- Purchase orders
- Multi-warehouse management
- Stock logs and history
- Low stock notifications
- Advanced reports
Smart Manager for WooCommerce
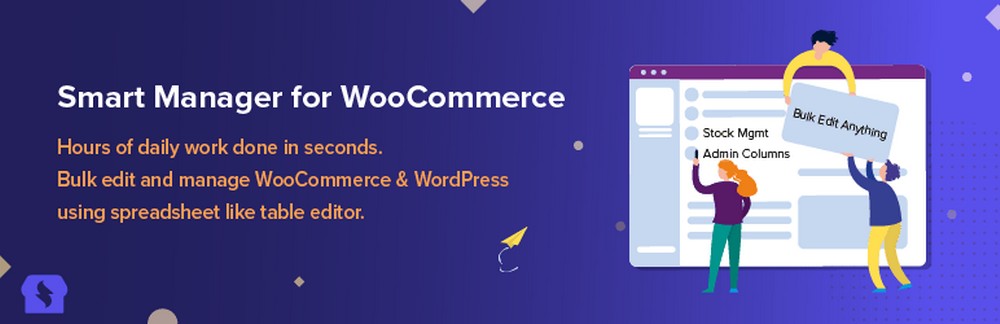
Smart Manager is a powerful plugin that enhances the management capabilities of your WooCommerce store.
While it provides various features for overall store management, it also includes inventory management functionality.
Notable features of Smart Manager:
- Spreadsheet-like interface
- Bulk actions
- Advanced search and filters
- Inline editing
- Import and export
- Variations management
- Sales analysis
WP Inventory Manager
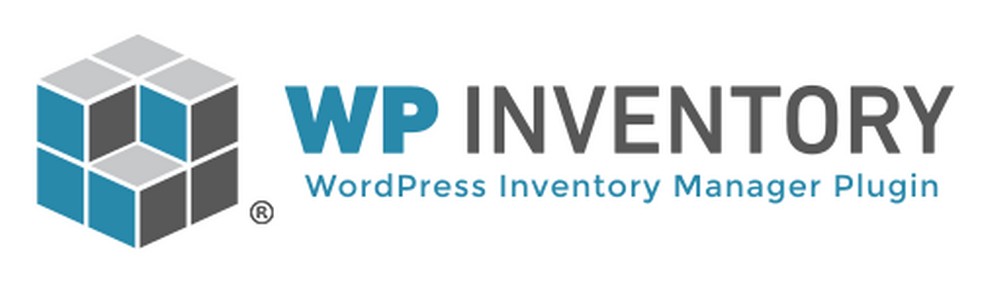
WP Inventory Manager is a dedicated inventory management plugin for WooCommerce. It offers features to track, control, and optimize your inventory effectively.
Key features of WP Inventory Manager:
- Inventory tracking
- Low stock notifications
- CSV import and export
- Inventory reports
- Product variations management
- Out-of-stock management
- Stock history and logs
WooCommerce Out of Stock Manager
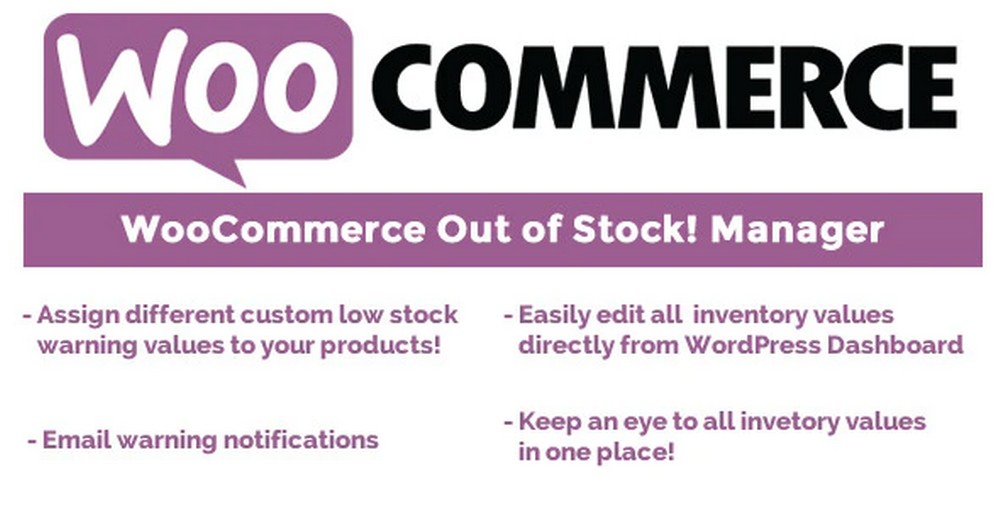
WooCommerce Out of Stock Manager is a plugin specifically designed to manage out-of-stock products in your WooCommerce store.
While its primary focus is on inventory control for out-of-stock items, it offers features to help you handle stock availability effectively.
Notable features of WooCommerce Out of Stock Manager:
- Out-of-stock product management
- Hide out-of-stock products
- Alternative product display
- Custom stock status messages
- Low stock notifications
- Email notifications
- Stock availability reports
Final words
Effective inventory management is crucial for the success of your WooCommerce store.
By implementing the right strategies and utilizing the available tools, you can streamline your inventory processes, prevent stockouts, and provide excellent customer service.
With the help of specialized inventory management plugins, you can streamline and optimize your inventory control processes.
Remember, efficient inventory management not only ensures smooth operations but also contributes to customer satisfaction, retention, and increased sales.
Take control of your inventory management today and unlock the full potential of your WooCommerce store!
WooCommerce Inventory Management – FAQs
Inventory management is crucial for WooCommerce stores as it ensures that products are available when customers place orders. It helps prevent stockouts, optimize inventory levels, reduce carrying costs, improve customer satisfaction, and streamline operations.
Some common challenges in WooCommerce inventory management include inaccurate stock counts, difficulty in syncing inventory across multiple sales channels, manual inventory updates, lack of real-time visibility, and inefficient order fulfillment processes.
To optimize inventory levels in your WooCommerce store, you can implement techniques such as setting reorder points and safety stock levels, utilizing demand forecasting, analyzing sales trends, implementing just-in-time inventory practices, and leveraging inventory management tools or plugins for automatic inventory updates.
Yes, you can integrate a warehouse management system (WMS) with WooCommerce to enhance inventory management. A WMS can automate inventory tracking, order fulfillment, and shipping processes, improve accuracy, provide real-time inventory visibility, and streamline warehouse operations for efficient inventory management in your WooCommerce store.
This is a guest article contributed by Tahsinul Hoque.
Tahsinul Hoque is a WordPress enthusiast and a writer with a keen interest in all things related to the web and technology. He enjoys writing about his experiences and sharing his knowledge with others in the community. When he’s not tinkering with websites or writing, you can find Tahsinul exploring new coffee shops and trying out new cuisines.